Diamond tools for shank type cutters
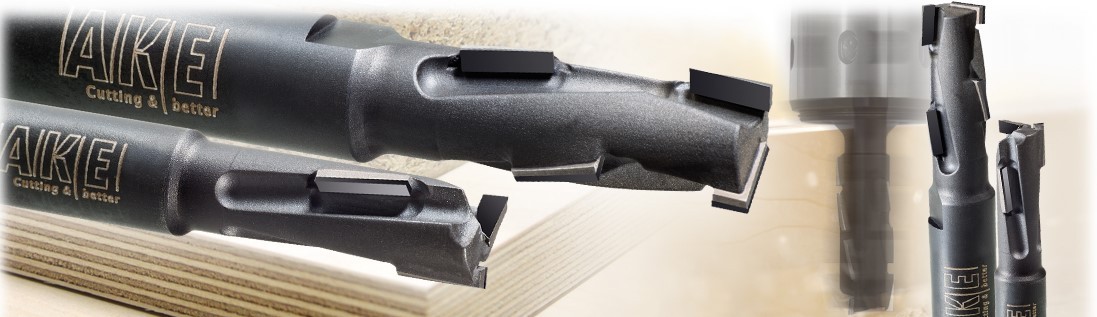
PCD shank cutters are available for sizing, jointing and profiling.
The standard range includes but is not limited to:- Blackline routers
- Z3 Router 2.0
- Harmony milling cutters
Blackline routers:
The AKE blackline routers are part of the latest generation of PCD end mills. "blackline" does not simply refer to the colour design of the tools, but also represents a tool that focuses above all on the balance between cost and benefit. The influencing factors in the development of this product range were robustness and tool life. This provides customers with a technically advanced entry-level PCD milling cutter for machining abrasive materials (chipboard/MDF, etc.).
Z3 Router 2.0:
The brand-new Z3 DP routers represent the pinnacle of high-performance PCD end mill technology. These are the first routers anywhere in the world developed using experience gained with Cutting 2.0. The results speak for themselves.
The teeth arrangements used up to now placed constraints on urgently needed advancements in surface quality, feed rates and tool life.
AKE has now managed to overcome these constraints. The result of this is a new and impressive appearance for the novel and highly uniform cutting edge geometry, with true Z3.
This enables both a reduction in repeated chip cutting and an increased feed rate with reduced power consumption.
In addition,the routers of the Cutting 2.0 generation feature exceptional operational smoothness. This results in excellent surface quality. An all-round cost-effective tool for formatting a wide range of materials.
Harmony milling cutters
"Harmony" has become a byword for PCD-tipped tools in the industry.
As with its jointing cutters for continuous production lines, AKE has created a variant of the successful HARMONY tools for machining on stationary machines. With this variant, operators have access to various milling cutters with diameters of between 6 mm and 80 mm.
One special feature of Harmony milling cutters is the large axis angle of the cutting edges. This enables edges and crosspieces to be milled through without causing tearing in many materials. Operators can expect impressive surface quality as a result.